SUPERIOR INDUSTRIAL HEAT TRANSFER SERVICES
Innovative Technology And Performance For The Canadian Industrial Market
Warco Industrial Heat Transfer offers its customers a very comprehensive, cost effective and safe heat exchanger program. One that is proven and allows customers to focus on their core business all the while knowing that their assets are being restored to the highest levels the industry has to offer.
Planning and execution:
- Warco offers its customers a single point of contact from the pre-planning sequence of events to deliverable job scope
- Isolation and blinding
- Bundle extraction, installation &transportation
- Our aerial extractors are late model Idrojet’s with a bundle weight capacity of up to 100,000 lbs.
- Our QC department works directly with our managers, clients and governing body to ensure all policies, procedures are the highest standards and reflect best practices of industry.
Heat Exchanger Bundle Transportation:
- Warco’s process allows for the loading of bundles directly from our bundle pullers onto specifically designed bundle hauling trailer.
- Our unique purpose-built bundle hauling trailer reduces the risk of injury and damage to customer assets and eliminates the risk of contaminant spills while in transit.
Heat Exchanger Bundle Cleaning:
Combining heat, chemistry, Ultrasonics, and high pressure in a controlled environment has provided our customers with significant cost saving, improved safety, reduced environmental liability and less waste. Returning heat transfer assets to full heat shed capacity allows for more efficient profitable operation. This is a game changer in heat transfer services
- Warco’s facility layout is designed in the most efficient manner to process equipment safely and expediently.
- Warco Industrial can help your business cut costs and downtime, our expertise in ultra-sonic and high-pressure cleaning ensure that your heat exchangers are cleaned to the highest levels possible increasing production and profitability..
- Our exchanger program is backed by customer testimonials and their confidence in awarding us with long term maintenance agreements.
- Our experience has allowed us to explore the use of new technology and implement best practices that have proven effective for our customers
- The thicker polymer deposits become, the longer and more difficult they take to clear using traditional methods. The importance of regular, routine cleaning and maintenance is made more efficient using Ultrasonic cleaning methods.
- Conventional high-pressure cleaning can use more than 20,000 Gal (76,000 litres) of water per exchanger and this wastewater requires treatment.
- Performing this service in our shop reduces the cost of high-pressure cleaning alone significantly and lowers the risk of serious injury to personnel. Our process combines ultrasonic cleaning and reduces environmental disposal waste on site.
- Warco offers a full array of cleaning methods that allows us to bring your process equipment back to the highest level of operational condition as quickly and as safely as possible.
Inspection Services:
- Warco doesn’t have inspections service but provides space in its cleaning facility to execute inspections by the customers chosen service provider. This further helps in maintaining scheduled downtime.
- Once inspections are completed bundles can be wrapped and transported or moved into the repair phase of the program.
Heat Exchanger Bundle Repairs:
- Another benefit to off site cleaning is when repair work is identified resources are often readily available reducing downtime.
- Warco is an ABSA registered heat exchanger repair specialist both in shop and field.
- All inspections and repairs can be completed in our shop with safety and efficiency by our technicians and 3rd party contractors, or firm of your choice.
Heat Exchanger installation, leak testing and handover:
- Upon completion of cleaning inspections and repairs Warco can complete the reinstatement process
- Bundle installation
- Bolt up, torque and tensioning
- Leak testing
- De-blinding
- Handover- ensure quality control handover and acceptance
- Reach out to gain feedback for program improvement
Other Work
Before & After
Ultrasonic Cleaning Technology
Ultrasonic cleaning particularly with thickness mode ultrasonic transducers provides a much more efficient way to clean heat exchangers. Sound wave implosions, called cavitation separates the contaminant from the surface without damaging a component. Warco Industrial expertly applies patented technology to achieve unparalleled results.
- Effectively removes all forms of hydrocarbon contamination and refinery-grade by-products compared to conventional cleaning processes.
- Cleans components and equipment once deemed unrestorable.
- Extending exchanger service and reducing cleaning cycles. Cleaner surfaces + Increased flow rates = Greater utilization.
- Ultrasonic cleaning reduces risk of injury to personnel and equipment compared to high pressure cleaning method alone.
- Superior cleaning efficiency of ultrasonics increases a facility’s uptime and reduces the total cost of ownership.
- Our process and technology have proven to increase flowrates, reduce risk and harm to personnel, and eliminate environmental liability to our customers.
High Pressure Industrial Cleaning
- When cleaning heat exchangers and other process equipment, it is important to remove all deposits and sediment, restoring assets to as close to like new condition as possible. Failure to remove all fouling will not deliver the benefits of this effort reducing the return on investment. Warco Industrial has the right people, processes, and tools to execute high pressure cleaning, whether it is on-site or off-site at our purpose-built facility. Our high-pressure operators receive industry recognized training and meet the requirement of Water Jet Technology Association (WJTA)
High Pressure Services
- Heat exchanger tube cleaning
- Heat exchanger shell cleaning
- Line and drain cleaning
- Flex lancing, as well as ridged lancing for cleaning fixed exchangers,
- Aerial cooler cleaning
- Evaporators
- Drill pipe cleaning
- Downhole screen cleaning
- Our portable self-contained high-pressure units supply 10,000 psi to 40,000 psi at various GPM
Our Work
Before & After
Field Mechanical Specialty Services
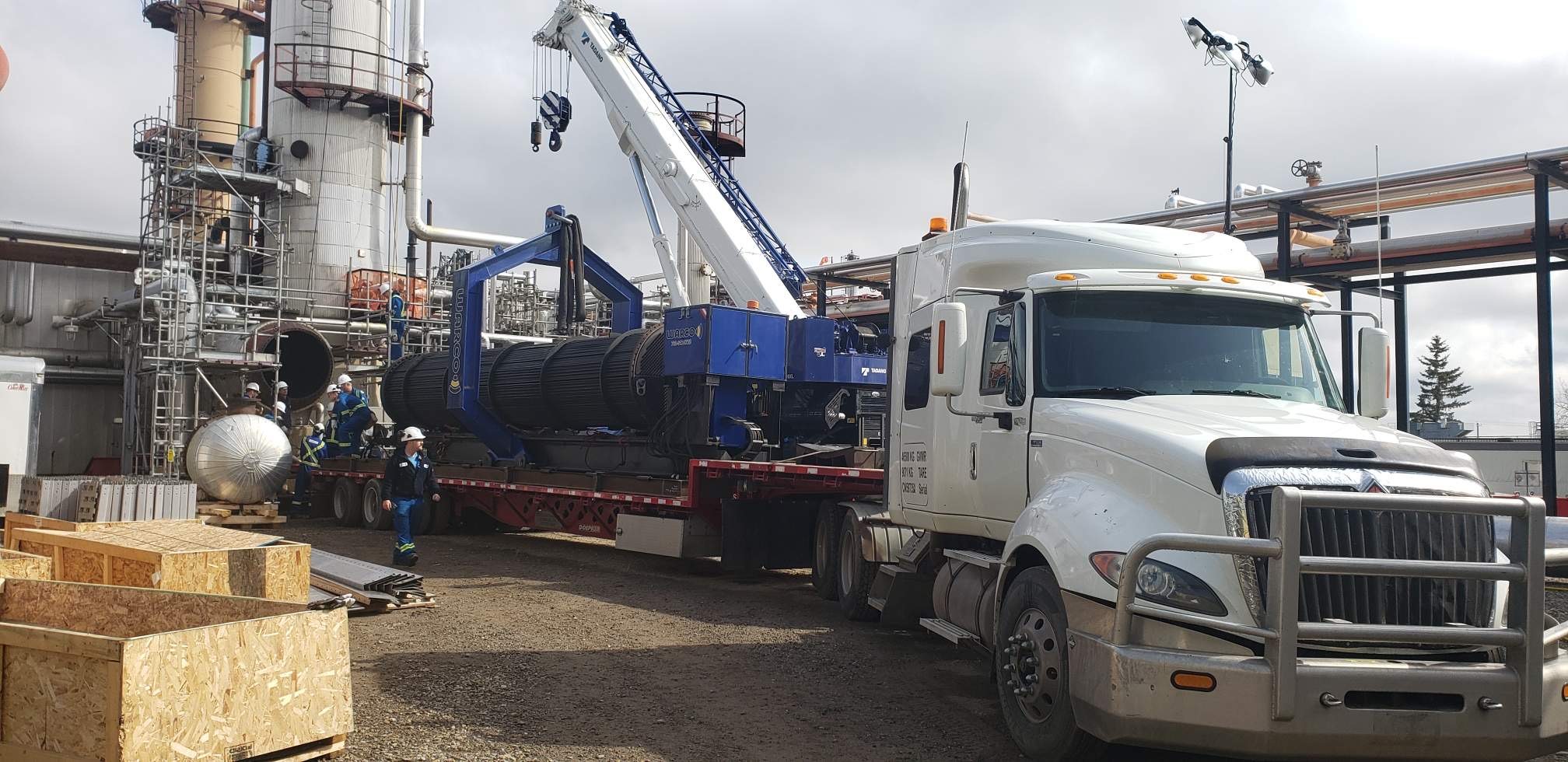
Warco Industrial is ABSA registered and is adept at completing a variety of mechanical services for both shop and field.
Warco provides year-round, skilled, and responsive trade support with the tools and equipment necessary for heat exchanger routine maintenance and turnarounds.
- Bundle Extraction
- Bundle Installations
- Equipment isolation and blinding
- Disassembly and reassembly of components
- Bundle repairs
- Jack and roll of equipment
- Bolt torquing and tensioning
- Air and hydro pressure testing
- Management of cleaning for bundles, components, and shells.
- Heat treatment, NDT, and Inspection.
- Heat exchanger repairs:
-
- Tube plugging
- Tube replacement
- Weld-overlay
- Gasket face repairs
- Completion of turnover documentation.
- Aerial cooler maintenance and repairs
- Field fabrication
- Flange facing, weld overlay and machining
- HSE representation
- On and off-site bundle transportation
- On site supervision
- Project planning
- QC management
- Qualified Tradespeople in all disciplines
Aerial Cooler Repair
- Header Box repairs
- Fin combing and Cleaning
- Aerial cooler tube repair
- Re-rolling
- Plugging and testing
- We complete replacement of parts for actuators, louvers, shoulder plugs and gaskets.
- Welding
- Tube replacements
- Inspection and testing
- Field service support
- These tasks include all required turn over packages for ABSA and customer upon job completion.
Aerial Cooler Cleaning
- Full service external fin and screen cleaning utilizing Warco’s air blasting method.
- Internal tube cleaning using high pressure water jetting technology.
Our Work
Before/After
Radiator Services
Our custom fabrication shop specializes in Cooling System fabrication and repair. We build complete radiator and cooling system packages tailored to meet the needs of any climate or industry.
Warco has expanded its service offering considerably to include comprehensive radiator repair, testing, replacement, and manufacturing. While a majority of Warco’s customers originate from the oil and gas sector we also service:
- Agriculture and ranching
- Heavy Industrial
- Light Industrial
- Automotive
- Vehicle restoration
- Bitcoin mining
- Forestry
- Mining
- Transportation Industry
- Custom Fabrications/applications
RECORE & REBUILDING
- Re-cores
- Re-builds
- Replacing plastic or brass tanks.
- Custom fabrication of steel, aluminum or stainless-steel bolt on tanks.
- Complete new hardware kits.
- Repairing tube damage in brass and aluminum cores.
- Replacing filler necks and hose connections.
- Tube rod out.
- Stock of popular cores.
- Replacement of in-tank oil coolers.
- Replacement of new sheet metal shrouds, side anchors or mounts.
- Restore flow of plugged radiator cores utilizing Ultrasonic cleaning technology
- We can respond to unique client needs by using a special core with tube protectors, steel fins, solder coated fins, header braces, etc.
- Re-cores backed by our warranty.
NEW REPLACEMENT:
- We offer new replacement radiators at competitive prices and with short lead times.
- Meeting OEM quality specifications
- Our service includes radiators for Detroit Diesel, Caterpillar, Cummins, Waukesha, and many others.
Our Work
Health, Safety & Environment
We take pride in being a safe company committed to taking care of our customers, our people and the environment.
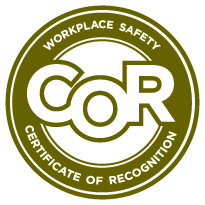
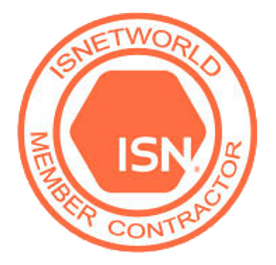
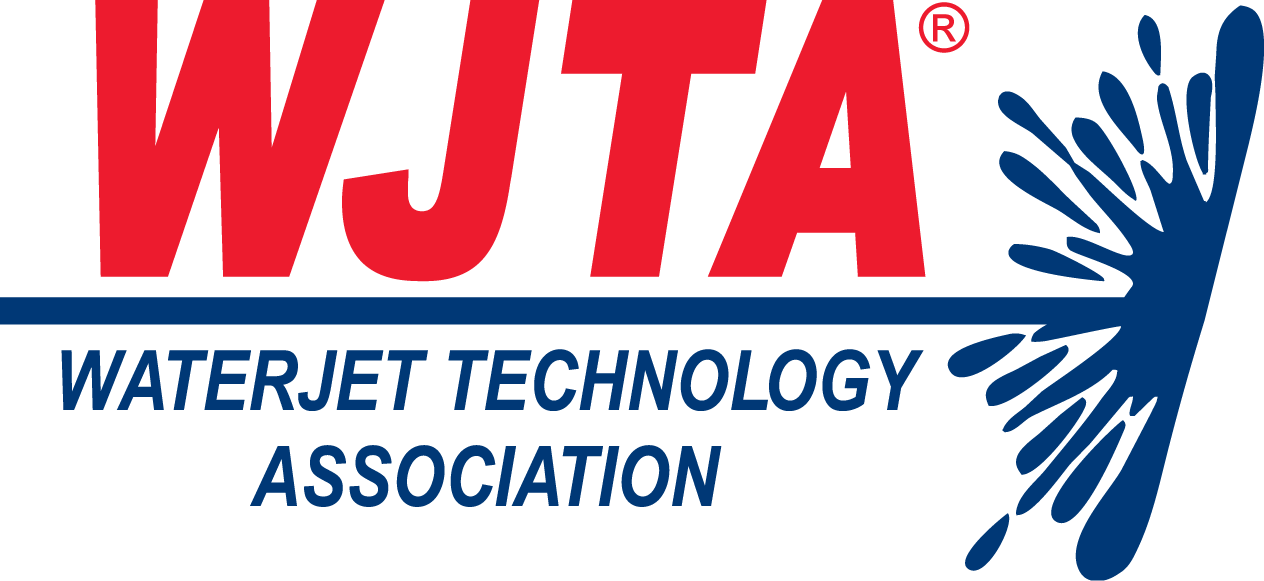